Porosity in Welding: Identifying Common Issues and Implementing Ideal Practices for Avoidance
Porosity in welding is a prevalent problem that frequently goes unnoticed till it creates considerable problems with the integrity of welds. This usual problem can compromise the toughness and longevity of bonded structures, posing safety and security dangers and resulting in costly rework. By recognizing the root causes of porosity and implementing reliable avoidance strategies, welders can considerably improve the high quality and reliability of their welds. In this conversation, we will explore the crucial elements contributing to porosity development, examine its destructive impacts on weld performance, and go over the most effective techniques that can be adopted to decrease porosity incident in welding procedures.
Typical Reasons For Porosity
Using dirty or wet filler products can present pollutants into the weld, adding to porosity concerns. To minimize these usual reasons of porosity, detailed cleansing of base metals, proper securing gas selection, and adherence to optimum welding specifications are vital practices in accomplishing top notch, porosity-free welds.
Effect of Porosity on Weld High Quality

The existence of porosity in welding can considerably jeopardize the structural stability and mechanical homes of bonded joints. Porosity produces voids within the weld steel, weakening its general strength and load-bearing capability. These voids function as stress and anxiety concentration factors, making the weld much more at risk to splitting and failure under applied loads. Furthermore, porosity can reduce the weld's resistance to rust and various other ecological variables, better reducing its durability and performance.
Welds with high porosity levels have a tendency to show lower influence strength and lowered capability to deform plastically prior to fracturing. Porosity can hinder the weld's capacity to successfully transmit forces, leading to early weld failure and potential security dangers in critical frameworks.
Best Practices for Porosity Avoidance
To enhance the architectural integrity and high quality of bonded joints, what details steps can be carried out to reduce the incident of porosity throughout the welding process? Porosity prevention in welding is vital to make certain the honesty and toughness of the last weld. One reliable practice appertains cleaning of the base steel, getting rid of any kind of impurities such as corrosion, oil, paint, or wetness that go to these guys can lead to gas entrapment. Making sure that the welding tools is in great problem, with clean consumables and suitable gas circulation rates, can likewise considerably decrease porosity. Additionally, maintaining a steady arc and regulating the welding criteria, such as voltage, current, and travel speed, assists develop a consistent weld pool that lessens the danger of gas entrapment. Using the right welding technique for the particular material being bonded, such as readjusting the welding angle and weapon position, can even more stop porosity. Normal inspection of welds and prompt remediation of any type of issues recognized throughout the welding procedure are essential practices to avoid porosity and create premium welds.
Significance of Appropriate Welding Strategies
Implementing correct welding strategies is extremely important in making sure the structural integrity and top quality of bonded read this article joints, developing upon the structure of effective porosity prevention actions. Too much heat can lead to raised porosity due to the entrapment of gases in the weld swimming pool. In addition, making use of the suitable welding criteria, such as voltage, current, and travel rate, is other essential for accomplishing audio welds with minimal porosity.
In addition, the option of welding process, whether it be MIG, TIG, or stick welding, ought to align with the details requirements of the task to make certain ideal results. Appropriate cleansing and prep work of the base steel, as well as choosing the appropriate filler product, are additionally necessary components of skillful welding techniques. By adhering to these best methods, welders can lessen the threat of porosity development and generate high-quality, structurally sound welds.
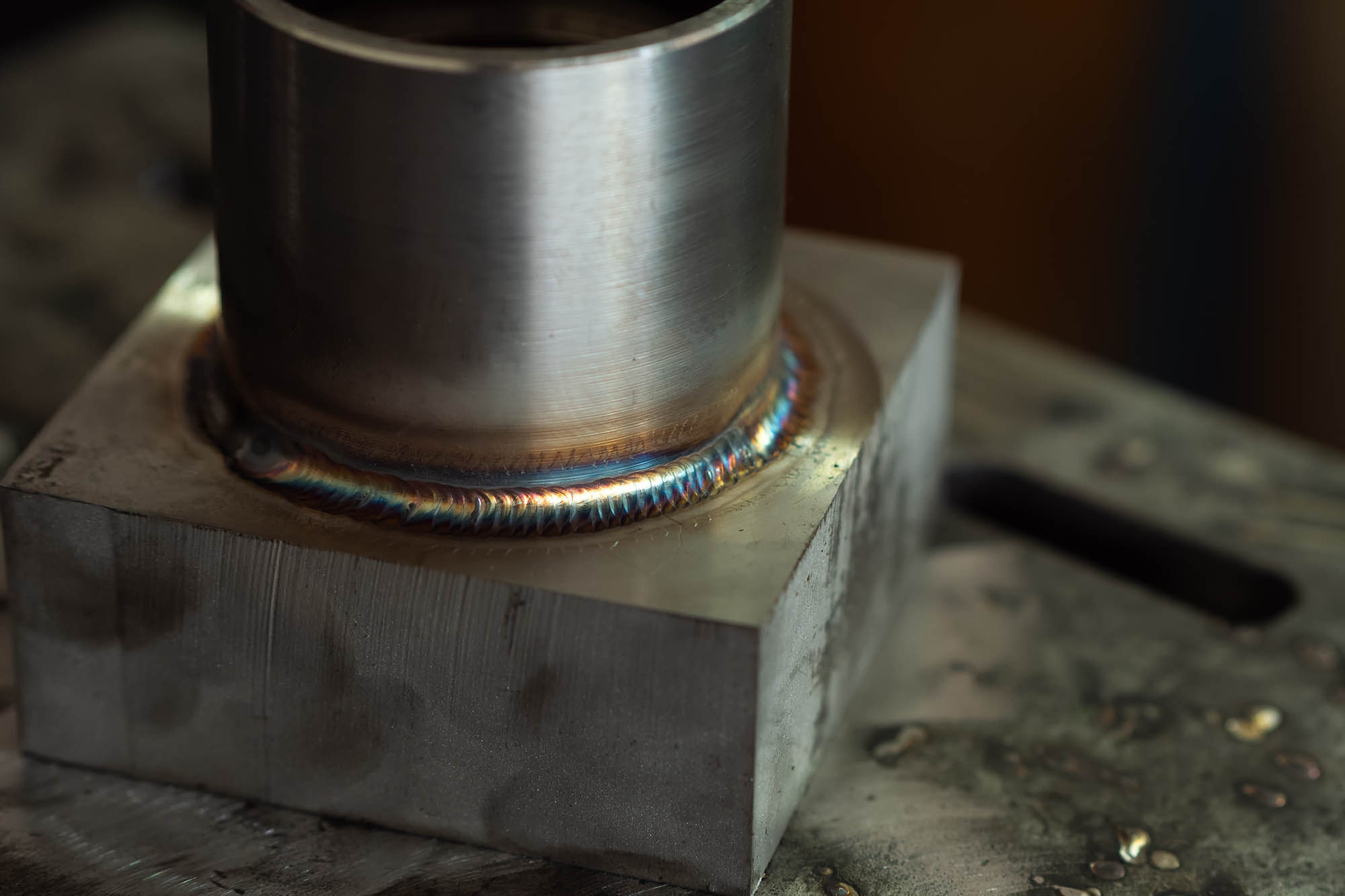
Checking and Quality Assurance Procedures
Quality assurance measures play a vital function in verifying the honesty and dependability of welded joints. Examining procedures are important to spot and stop porosity in welding, making certain the strength and sturdiness of the end product. Non-destructive testing methods such as ultrasonic screening, radiographic screening, and aesthetic inspection are commonly employed to identify possible defects like porosity. These techniques allow for the evaluation of weld high quality without endangering the integrity of the joint. What is Porosity.
Post-weld inspections, on the various other hand, assess the final weld for any kind of defects, including porosity, and confirm that it meets defined criteria. Carrying out an extensive quality control strategy that consists of complete testing procedures and examinations is paramount to minimizing porosity concerns and ensuring the general high quality of welded joints.
Verdict
In final thought, porosity in welding can be a common concern that affects the quality of welds. By recognizing the typical root causes of porosity and implementing best methods for prevention, such as appropriate welding strategies and screening actions, welders can make certain top quality and dependable welds. It is vital to focus on prevention techniques to minimize the event of porosity and maintain the honesty of bonded frameworks.